In June of 2023, 3M agreed to a historic $10.3 billion settlement concerning PFAS, a class of harmful “forever chemicals” used in everything from nonstick frying pans to takeout containers to firefighting foam.
3M will pay out the settlement to any city and county water system in the US that finds PFAS in its waters–and to many utilities, that funding will provide desperately-needed capital to update infrastructure and equipment.
But there’s a catch: much of the funding comes with strict data and reporting requirements. You have to prove there’s PFAS in your system first, and that’s easier said than done, especially if your industrial user sampling and monitoring programs aren’t organized or up to date.
Whether you’re using Klir, other software, or even spreadsheets to manage your pretreatment programs, we believe these developments underline the importance of sound data management.
Bringing together crucial sampling information is important in more than just the typical enforcement action scenario, where a regulator steps in to fine a polluter. It can also mean the difference between benefitting from a historic settlement and missing out on millions in funding.
Not sure your pretreatment program has all the tools it needs? Here’s a step by step guide detailing all of the data it needs to capture and track to be successful.
Defining the Data Management Challenge
Industrial pretreatment programs can vary a lot depending on any particular industrial user’s situation, their NPDES permit, and the pretreatment permit issued by that user’s utility.
While Federal and State EPA are responsible for enforcement, much of the work involved in administering a pretreatment program ultimately falls on the shoulders of utilities, who must:
- Maintain an inventory of industrial users, permits and surcharges
- Prepare monitoring programs and track progress of compliance monitoring
- Generate and submit reports to regulators
- Manage violations and issue notifications to customers
This means that while pretreatment is ultimately an engineering challenge, there’s an equally important administrative and project management challenge utility managers have to tackle.
For larger utilities, this might involve many moving parts, including: site visits and inspections, customer information, sampling data, industrial user-provided records and data, etc all of which have to be stored and tracked.
It’s also a tricky balancing act: utilities must maintain good relationships with industrial customers while ensuring they stay on top of their obligations, and also pay attention to important changes in discharges, which can be difficult to do when all you have to look at are spreadsheets–or worse, physical log sheets.
When it comes time to enforce rules or get industrial users to comply with new regulations—as is the case with 3M and PFAS—utilities also need meticulous and complete records that regulators can rely on during an enforcement action.
From our perspective, the best way to achieve all of this is by building an airtight data management process that gives customers, utility workers and regulators access to reliable information quickly.
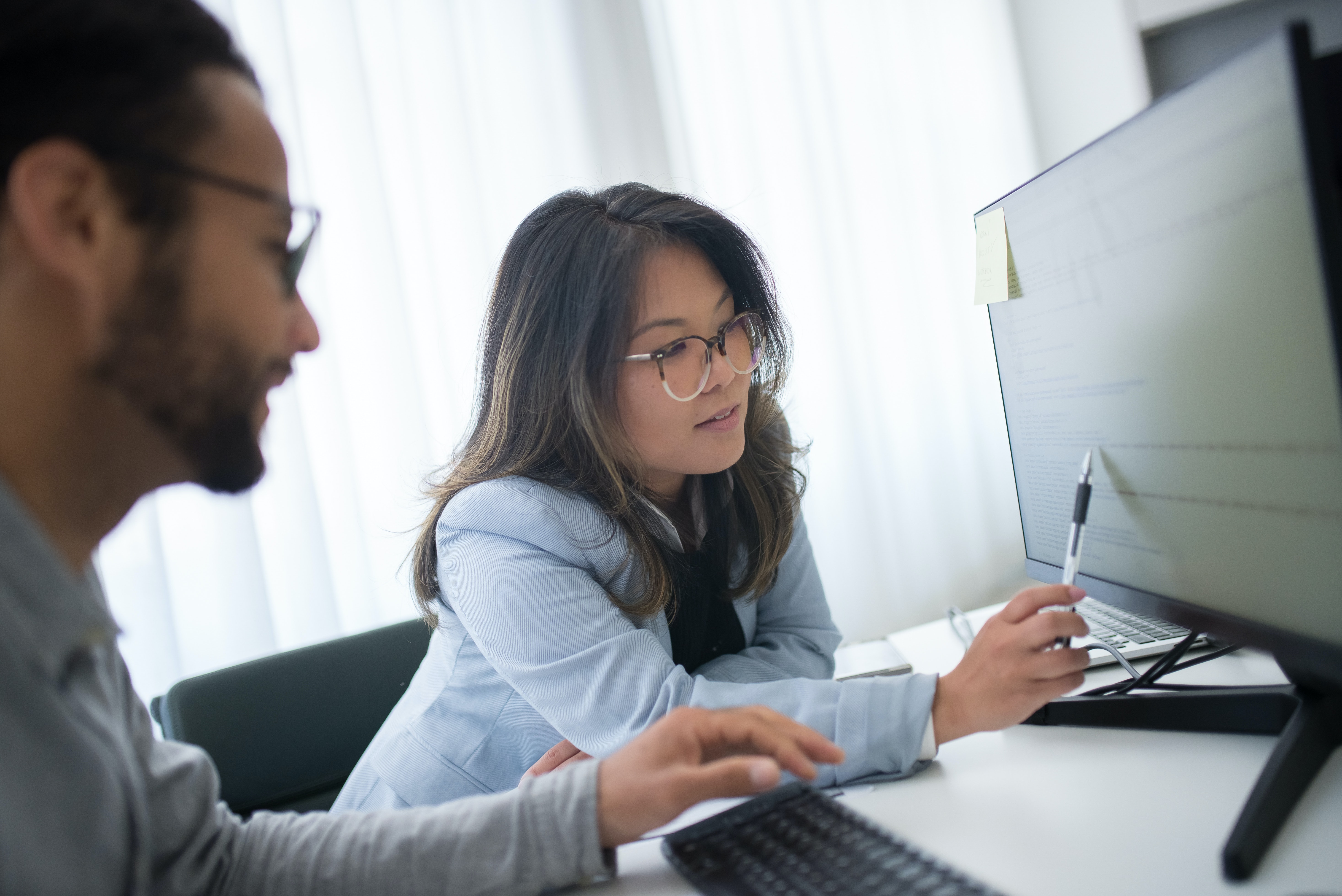
Step 1: Build a Digital Industrial User Inventory
The first step to building a successful pretreatment monitoring system is to build a master list or ‘inventory’ of industrial users.
Whether you’re building an inventory from scratch or just making sure your existing one is accurate, it’s important to keep it updated by regularly surveying documents like:
- Water billing records
- Business licenses
- Building permits
- Sewer connection permits
- Commercial directories
- Property tax records
- Fire Department emergency management plans and records
- Applications for water or wastewater service
Other sources that might be useful for updating and keeping industrial user inventories current include:
- Enforcement and Compliance History Online (ECHO)
- RCRA information, the Discharge Monitoring Report Pollutant Loading Tool, the Toxics Release Inventory, as well as the state’s hazardous waste generators list
- Your local chamber of commerce and other agencies such as utilities, code enforcement, health departments, and fire departments
If you just recently added a new user to the list, you might also want to send them a survey to gather more information, or schedule an in-person visit.
What Should My User Inventory Include?
In addition to basic information–ie: the company name, address of facility, name of a primary contact person, and the type of business or manufacturing process the company engages in–you’ll have to include important information about how each user connects to the water system and what they typically discharge, including:
- Estimates of water usage and process water discharged
- Types of hazardous wastes generated and how they’re disposed of
- NAICS codes,SIC codes and CFR 40 codes if required
- Process wastewater flow
You’ll also need to document the steps and procedures each user takes to fulfill their pretreatment obligations, including a description of existing on-site pretreatment facilities, a list of all environmental permits held by the discharger, and which pretreatment standards the user is subject to.
To save time, many utilities will update this information by completing regular surveys of all industrial users in their system. The Oregon Department of Environmental Quality has some helpful guidance for utilities looking to increase response rates to Industrial User Surveys, including:
- Develop an outreach strategy, and contact each facility before sending the survey form if you can, so they know it’s a legitimate and important request.
- Include a stamped, pre-addressed envelope for returning the completed survey, or label them such that when they’re folded they’re ready to send back through the mail.
- Make sure to request any address changes, in case any facility has moved.
Further Reading: Industrial User Survey Guidance - State of Oregon Department of Environmental Quality
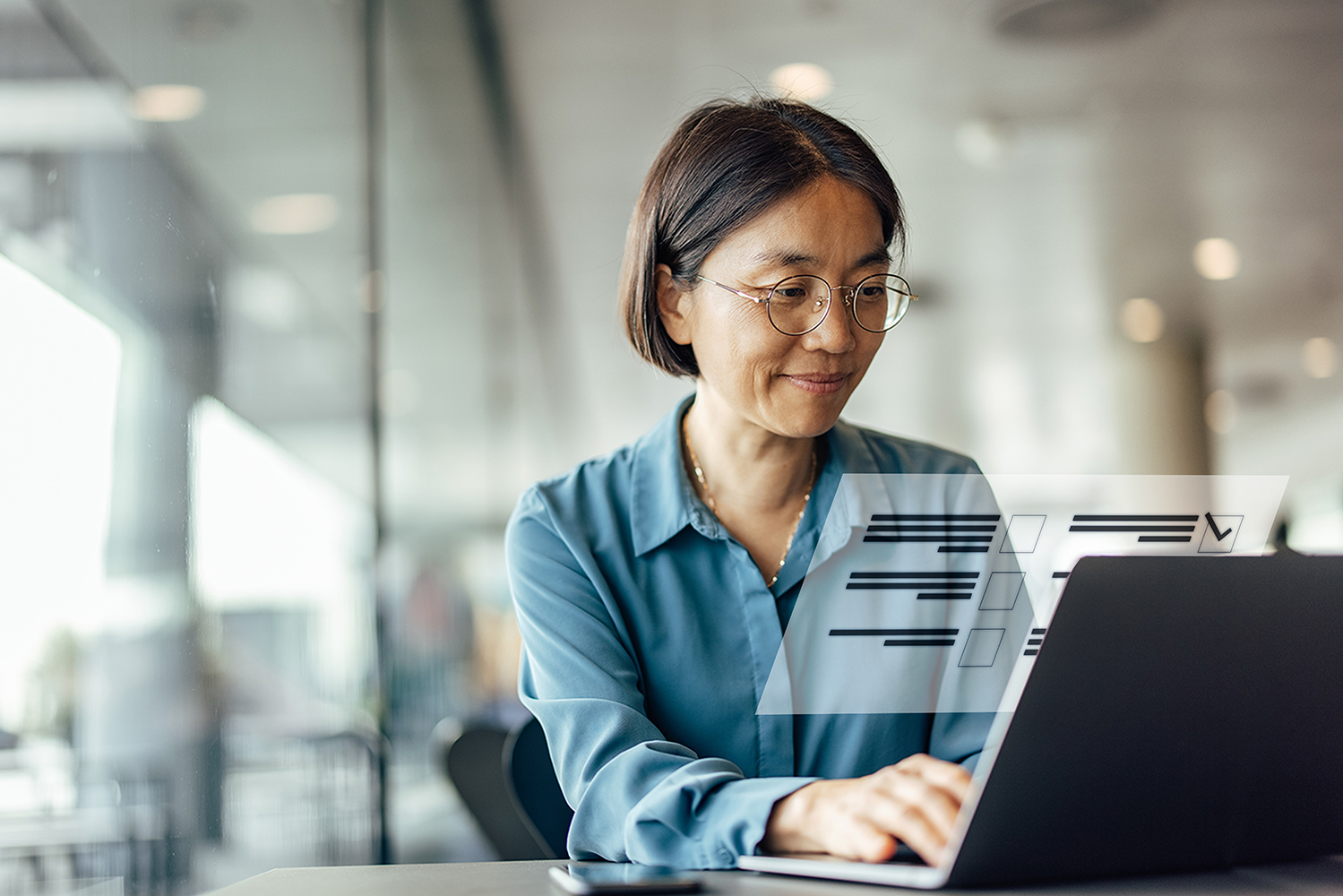
Step 2: Build or Onboard a Streamlined Pretreatment Program Management System
Building a comprehensive list of users is important, but it’s just the first step in tackling the industrial pretreatment data management challenge.
According to the EPA, utilities also need to maintain robust procedures for tracking industrial user problems, and the best way to do that is by making sure all files and records are available and up to date in an internal information management system like Klir.
Building a Data Management System: a Checklist
At minimum, the system you use to manage these processes should be able to capture the following:
- Basic user contact information and all previous correspondence
- Permits and permit applications
- Any previously completed industrial waste questionnaires
- Monitoring data and inspection reports
- Records of pending and previous surcharges
- Engagement from IUs via a CROMERR-ready self-serve portal
These procedures should help you quickly identify areas that may require follow up activity, and provide background information on the facility that can be reviewed prior to conducting inspections at the facility.
If an inspector takes effluent samples as part of a site visit, for example, there should also be an easy way for them to upload them into the utility’s compliance tracking system and quickly determine whether there’s been a violation.
In addition to simply capturing and storing certain types of information, your system also needs to actively track and manage certain key variables and dates, including:
- Due dates for compliance submittals
- Compliance violations and enforcement activities
- User compliance history
- Calculations for local limits and user limits for compliance
Remember that field notes, checklists, records of inspections, investigations, samples collected, and related inspection information can each also become an important part of the evidence package used by the utility in an enforcement action, and can even be entered in court as evidence if properly maintained.
In addition to records for industrial users, your IPP management system should also keep records pertinent to the administration of the utility’s pretreatment program itself, including:
- Documents establishing legal authority
- Pretreatment program approval and modifications.
- Copy of the POTWs own NPDES permit
- Applicable federal and state regulations
- Local Limits development documentation
- Enforcement response plans
- Correspondence between POTW and the Approval Authority and EPA
- Public notices
While utilities have typically handled all of this information using spreadsheets, Klir manages all of this data for you in a centralized system that pings you if something goes wrong, removing a huge layer of stress and work from the process of managing your industrial users.
Step 3: Generate and Submit Reports to Regulators
Probably the biggest help a system like Klir can provide when it comes to managing industrial pretreatment programs is the ability to quickly synthesize data and generate reports.
Under NPDES, POTWs are responsible for submitting an annual pretreatment program report, which should include basic information like:
- An updated list or inventory of Industrial Users
- Which pretreatment standards the user is subject to
- A summary of the status of user compliance over the reporting period
These reports should also provide an up to date and accurate record of any regulatory actions the utility took over the last year, including:
- A summary of compliance and enforcement activities (including inspections)
- A summary of changes to the utility’s pretreatment program that have not been previously reported
- Any other relevant information requested by the approval authority
Compiling and submitting these reports can be a time-consuming process, and within a few years most utilities will be required to submit them digitally through the EPAs eReporting rule. Depending on your state, it may be through the same portal you submit your NetDMR through, the Central Data Exchange, or some other online portal.
.png)
How Klir Can Help
Klir Comply gives water utilities a single source of truth to centralize, streamline and automate their compliance program so they can reduce the risk of missing something important and drive operational efficiency. Industrial pretreatment is only the beginning of Klir Comply for Community. We innovate based on customer and market input. Join us in shaping the future of sustainability and fulfilling the vision of having an all-in-one operating platform for water management. Our Customer Success team is on standby to partner in your digital transformation journey.